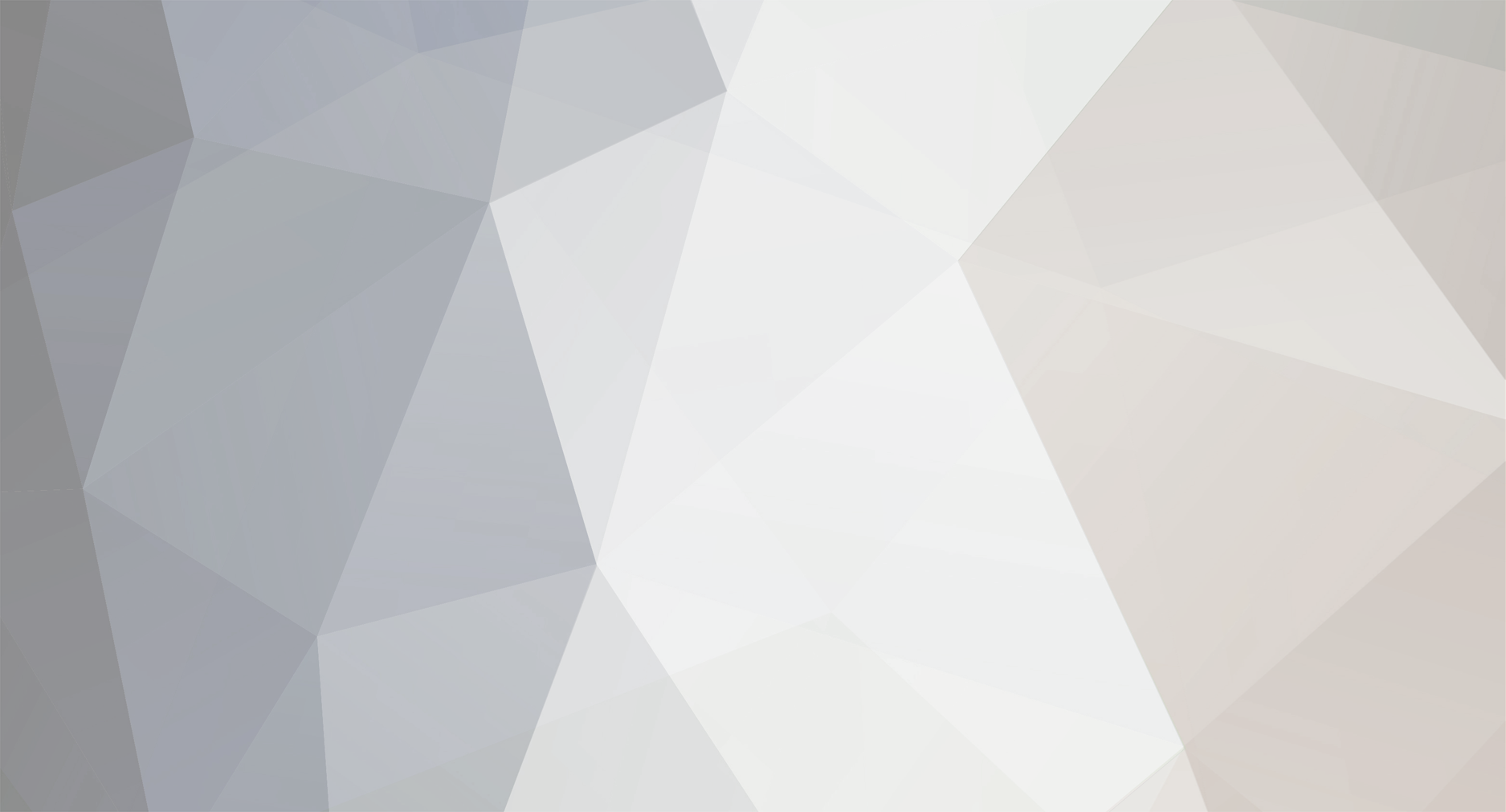
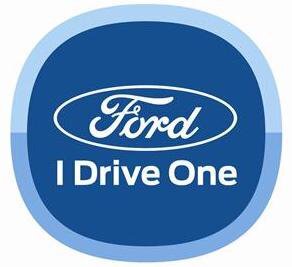
Haz
Edge Member-
Posts
1,460 -
Joined
-
Last visited
-
Days Won
392
Content Type
Profiles
Forums
Gallery
Everything posted by Haz
-
Battery monoriting reset
Haz replied to Larry's topic in Alarms, Keyless Entry, Locks & Remote Start
Specific to your question about how to accomplish a Battery Monitoring System (BMS) reset without use of a scan tool, I have edited a portion of the 2013 Edge-MKX Workshop Manual to provide you the answer... If the reset is not carried out [using a scan tool] it takes approximately 8 hours for the BCM to learn the new battery state of charge. During this 8 hour period, the vehicle must be undisturbed, with no doors opened or keyless entry button presses. If the vehicle is used before the BCM is allowed to learn the new battery state of charge, engine off load shedding can still occur and a message may be displayed. The full Workshop Manual section from which this brief passage, which describes the entire Battery Management System and the proper connection of an external battery charger, can be downloaded using the following link... Charging System - Principles of Operation - 2013 Edge-MKX Workshop Manual.pdf While not mentioned in the document, it would not hurt to begin the 8 hour undisturbed period by fully locking the vehicle, which most promptly allows the vehicle's electronic modules to power down into their 'sleep' state. Good luck! -
The following newly released Special Service Message describes factory-installed cornering capability of fog lamps on 2021-2022 Bronco Sport and 2021-2023 F-150... SSM 51428 2021-2022 Bronco Sport And 2021-2023 F150 - Cornering Lamps Feature Operation On 2021-2022 Bronco Sport and 2021-2023 F-150 vehicles, the cornering function in the fog lamp illuminates the inside of a corner when turning the steering wheel. If the steering wheel is slightly turned left or right with the headlamp switch on, the cornering function will activate. The fog light will be activated in the direction the steering wheel is positioned, even if fog light switch is off. This is an operating characteristic to improve customer visibility while turning. Do not attempt diagnosis or repairs or submit a claim for this condition. This function is independent of fog lamp operation. During pre-delivery inspection (PDI) fog lamp proper function verification, make sure steering wheel is positioned straight forward to cancel the cornering lamp function. Description of the cornering lamps feature in the 2022 Bronco Sport Workshop Manual is fairly brief... Cornering Lamps The fog lamps have a cornering function in which under certain conditions and inputs either lamp might turn on or off independently to aid visibility during cornering. The cornering lamps illuminate the inside of a corner when turning the steering wheel. If the steering wheel is slightly turned left or right with the headlamp switch on, cornering function will activate. The fog light will be activated in the direction the steering wheel is positioned, even if fog light switch is off. This is an operating characteristic to improve customer visibility while turning. This function is independent of fog lamp operation. Description in the 2021 F-150 Workshop Manual is more substantial... Cornering Lamps - Except Electric Vehicles The fog lamps have a cornering function in which under certain conditions and inputs either lamp might turn on or off independently to aid visibility during cornering. The cornering lamps illuminate the inside of a corner when turning the steering wheel or if a turn signal is active. If the steering wheel is slightly turned left or right with the headlamp switch on, cornering function will activate. The fog light will be activated in the direction the steering wheel is positioned, even if fog light switch is off. This is an operating characteristic to improve customer visibility while turning. This function is independent of fog lamp operation. The front corning lamps will illuminate when the following conditions are met: The vehicle is running The headlamp low or high beams are on (except as a feature of the DRL ) The vehicle speed is less than 40 km/h (25 mph) (if the vehicle exceeds 40 km/h (25 mph), vehicle speed must drop below 36 km/h (22 mph) to re-enable the cornering lamps) The turn signal is activated or the steering wheel is turned more than 35 degrees. The front corning lamps will turn off when the following conditions are met: The vehicle is not running The headlamps are off The vehicle speed is greater than 40 km/h (25 mph) The turn signal is deactivated or the steering wheel angle is more than 35 degrees then the steering wheel angle is less than 25 degrees. So, while I first thought fog lamp cornering illumination would only be triggered by turn signal operation, the factory function also employs Steering Wheel Position Sensor data to secondarily trigger the feature. The 2020 Edge Workshop Manual offers this description of that component... Steering Wheel Rotation Sensor On vehicles equipped with active park assist, the steering wheel rotation sensor is connected to the SCCM . The steering wheel rotation speed, angle and direction of travel is derived based on the position of the steering wheel position sensor and is sent to the ABS module over the HS-CAN2 . On vehicles not equipped with active park assist, information from the wheel speed sensors, PSCM and RCM are used by the ABS module to determine steering wheel angle when the vehicle is driven after initial start up. The ABS module uses the information received to calculate the steering center and save the information in memory. Then, using the information provided from the PSCM along with the saved center data, the ABS module determines the steering angle. The ABS module must re-learn the steering center whenever power is lost, for example during service when the battery is disconnected. To re-learn the steering center, the vehicle must be driven over 20 km/h (12 mph) for at least 1 minute on a fairly straight road. Good luck!
-
Welcome to the Forum, Justin! Hopefully, the Honda dealership is willing to address the issues you describe at no cost to you, if only they were informationally equipped to correct them. So, whether they or you are going to restore your son's Edge to smooth operation, the following information and documents should be helpful. If you have not already, you may want to review Stalling at red lights, anyone ever fixed this? about Forum member Carnye's 2013 2.0L EcoBoost Edge showing comparable symptoms. The following downloadable documents explain the Evaporative Emission system components, including the Canister Purge Valve and the Evaporative Emission Canister that dabangsta mentions... Document Download Links> Evaporative Emissions - Description and Operation - 2013 Edge Workshop Manual.pdf Evaporative Emission Canister Purge Valve — 2.0L Ecoboost - Removal and Installation - 2013 Edge Workshop Manual.pdf Evaporative Emission Canister - Removal and Installation - 2013 Edge Workshop Manual.pdf Evaporative Emission Canister Vent Solenoid - Removal and Installation - 2013 Edge Workshop Manual.pdf Fuel Vapor Tube Assembly - Removal and Installation - 2013 Edge Workshop Manual.pdf Diagnostic Pinpoint Test HX - Evaporative Emission (EVAP) System and Monitor - 2013 Ford Gasoline PC-ED Manual.pdf The following information and downloadable documents from the 2013 Edge Workshop Manual relate to the Edge's Active Grille Shutter System... Active Grille Shutter System The active grille shutter system (when equipped) is comprised of the grille shutter assembly and the grille shutter actuator. The active grille shutter system is primarily used to maximize fuel economy by reducing aerodynamic drag on the vehicle. In addition, the system is used to control coolant temperature, HVAC system performance and exhaust emissions depending on the vehicle speed. The system is also used to shorten engine warm-up time, increasing engine efficiency and providing heat to the vehicle occupants in a timely manner. PCM inputs/outputs used for controlling the active grille shutter system are the: Engine Coolant Temperature (ECT) sensor Intake Air Temperature (IAT) sensor A/C pressure transducer Accelerator Pedal Position (APP) sensor ABS module, messages sent over the High Speed Controller Area Network (HS-CAN) Engine cooling fan motor Engine oil temperature Grille Shutters The grille shutters are several "slats" or "blinds" connected to one another by a linkage system. One of the individual grille shutters is fixed to the grille shutter actuator. When the grille shutter actuator moves, it moves the attached shutter which causes the other linked shutters to move. The individual grille shutters are not available for service separately, they are serviced with the grille shutter assembly. Grille Shutter Actuator The grille shutter actuator is a smart motor which receives position requests from the PCM via a Local Interconnect Network (LIN) . One of the grille shutter blinds connects to the grille shutter actuator using a retainer. The grille shutter actuator can be serviced individually or as an entire assembly, which includes the grille shutters, grille shutter actuator, retainer and grille shutter housing. The grille shutter actuator positions the grille shutters based on commands received from the PCM. The full range of movement of the grille shutter actuator is a total of 90 degrees from fully closed to fully open. The actuator moves the grille shutters to 1 of 16 positions (approximately 6 degrees between positions) when requested by the PCM. Principles of Operation When the engine is turned off, the grille shutter actuator moves the grille shutters to the full open position. When the engine is started, a calibration of the grille shutter system occurs, which typically takes 15-20 seconds. The grille shutter system performs the calibration sequence by moving the actuator and shutters through their full 90 degree sweep to detect the end positions (open/close). The calibration sequence can begin in either direction, open or closed, and continues until it is successful or a fault is detected. It is possible for a long pause to occur between the 2 portions (open/close) of the calibration sequence. Calibration of the grille shutter system cannot be manually requested, it only occurs as determined by the grille shutter actuator. If certain faults are present (such as shutter blocked or actuator error) a recalibration is initiated in an attempt to resolve the concern. If the concern is not resolved after 3-4 attempts, a DTC is set in the PCM. Other faults also trigger a recalibration request, but not until a grille shutter DTC is set in the PCM. The Local Interconnect Network (LIN) supports bi-directional communication between the grille shutter actuator and PCM, allowing the grille shutter actuator to communicate position and fault information to the PCM. The PCM reports grille shutter system DTCs after the fault information is communicated by the grille shutter actuator for a predetermined amount of time. Any failures of the LIN for over 10 seconds continuously, results in the grille shutter actuator moving the grille shutters to the full open position. There is no indication to the driver that a fault with the grille shutter system is present or that a grille shutter system DTC is set in the PCM. Normal Operation The grille shutter actuator receives fused battery voltage from the Battery Junction Box (BJB) . When the engine is started, the actuator carries out a calibration test that can take up to 20 seconds to complete. During this calibration test the actuator moves the shutters through their complete range of motion from full open to full close. If the actuator cannot reach either position, cannot move at all, senses low voltage input or detects an internal short or open, the actuator sends a message to the PCM over a Local Interconnect Network (LIN) indicating a fault. After receiving a fault message for a predetermined amount of time, the PCM sets a DTC. Visual Inspection Chart Mechanical Electrical Grille shutter actuator Grille shutters Battery Junction Box (BJB) fuse 70 (10A) Grille shutter actuator Wiring, terminals or connectors Active Shutter Actuator Wiring Diagram Underhood Battery Junction Box Fuse 70 Location Document Download Links> Active Grille Shutter System - Description and Operation - 2013 Edge Workshop Manual.pdf Active Grille Shutter System - Diagnosis and Testing - 2013 Edge Workshop Manual.pdf Grille Shutter Actuator - Wiring Diagram - 2013 Edge Workshop Manual.pdf Grille Shutter Actuator - Connector C1651 Details - 2013 Edge Workshop Manual.pdf Battery Junction Box - Fuse-Circuit Breaker-Relay Location Illustration - 2013 Edge Workshop Manual.pdf Grille Shutter Assembly - Removal and Installation - 2013 Edge Workshop Manual.pdf Grille Shutter Actuator - Removal and Installation - 2013 Edge Workshop Manual.pdf Front Bumper Cover Assembly - Exploded View - 2013 Edge-MKX Workshop Manual.pdf Front Bumper Cover - Removal and Installation - 2013 Edge Workshop Manual.pdf Good luck!
-
This GSB 23-7034 has been superseded by GSB 25-7000, which is posted below... GENERAL SERVICE BULLETIN Interior Trim Concern Analysis 23-7034 08 March 2023 This bulletin supersedes 22-7055. Summary This article supersedes GSB 22-7055 to update the vehicle model years affected and Service Information. Use this document to assist in determining warrantable interior trim and steering wheel conditions. Service Information For fabric, carpets, cloth seats, safety belts, and interior trim: • Re-adhering loose leather to the steering wheel can be completed per the Workshop Manual • Do not use cleaning solvents, bleach or dye on the vehicle’s safety belts, as these actions may weaken the belt webbing • Remove dust and loose dirt with a vacuum cleaner • Remove light stains and soil with Motorcraft products as instructed in the vehicle Owner’s Manual • Do not use household cleaning products or glass cleaners, which may damage the finish of the instrument panel, interior trim and cluster lens, and can stain and discolor fabric • Avoid cleaners or polishes that increase the gloss of the upper portion of the instrument panel. The dull finish in this area helps protect you from undesirable windshield reflection • Make sure to wash or wipe hands clean if they have been in contact with certain products such as insect repellent and suntan lotion in order to avoid possible damage to the interior • Do not allow air fresheners and hand sanitizers to spill onto interior surfaces Non-warrantable conditions: • Interior damage • Scratches • Soiling, obvious vandalism or abuse • Pry marks • Damage, burns, soil marks, cuts, scratches, scuffs, tears or punctures • Damage due to chemicals, solvents, or use of non-Ford approved cleaners • Leather/stitching damaged during removal of steering wheel wrap • Leather/vinyl normal deterioration and wear • Wood natural grain pattern variation (i.e. grain direction, frequency, knots) • Dye transfer from customer clothing Cuts, Scratches, Scuffs, Tears Or Punctures (Non-warrantable) (Figures 1-3) Figure 1 Figure 2 Figure 3 Bubbles (Warrantable) (Figures 4-6) Figure 4 Figure 5 Figure 6 Stains From Chemical Influence (Non-warrantable) (Figures 7-9) Figure 7 Figure 8 Figure 9 Broken Attachments (Non-warrantable) (Figure 10) Figure 10 Alignment, Fit, Warped (Warrantable) (Figures 11-13) Figure 11 Warped instrument panel (Warrantable) (Figure 12) Figure 12 Warped glove box door (Warrantable) (Figure 13) Figure 13 Stained Headliner (Non-warrantable) (Figure 14) NOTE: Staining as the result of a defect would be covered as related damage. Figure 14 Rough Cut Headliner, Normal Appearance (Non-warrantable) (Figure 15) Figure 15 Creased Headliner (Non-warrantable) (Figure 16) Figure 16 Headliner Edge Visible (Warrantable) (Figure 17) NOTE: Complete removal/installation may be required to ensure proper alignment. Figure 17 Loose Mat Anchor (Warrantable) (Figure 18) NOTE: With no associated liquid staining present. Figure 18 Loose Carpet (Warrantable) (Figure 19) NOTE: Compete removal/installation may be required to establish a proper fit. Figure 19 Stains (Non-warrantable) (Figure 20) NOTE: Abrasive liquid may dissolve carpet fibers. Figure 20 Carpet Matted Appearance (Warrantable) (Figure 21) NOTE: This appearance may be the result of depressed fibers. This can be corrected by cleaning and reanimating the fibers using a carpet/steam cleaner (with temperatures under 350 degrees Fahrenheit) in the area. If a carpet/steam cleaner is not available, this procedure can be sublet out to a local interior/detail shop. If a shop is not locally available, a steamer such as Rowenta steamer or equivalent can be purchased and used to correct this condition. This tool purchase should be claimed as an outside service part (OSP). Figure 21 Carpet Cut (Non-warrantable) (Figure 22) Figure 22 Carpet Edges Fraying (Non-warrantable) (Figure 23) NOTE: Carpet edges are considered an unfinished edge and fraying at the edges is a normal appearance (frayed fibers can be trimmed for satisfaction) and does not require carpet replacement. Figure 23 Carpet Pile Appearance (Non-warrantable) (Figures 24-25) Frayed appearance can be corrected by mild brushing of the pile in a forward direction. This would be considered part of vehicle care and not eligible for warranty. (Figure 24) Figure 24 Frayed appearance on left side of image can be corrected by mild brushing in a forward direction as seen on the right side. (Figure 25) Figure 25 Leather Steering Wheel Worn Or Peeling (Warrantable) (Figure 26) Figure 26 Urethane Steering Wheel Worn Or Peeling (Warrantable) (Figure 27) Figure 27 Steering Wheel Abrasion (Non-warrantable) (Figure 28) Figure 28 Urethane Steering Wheel Mold Marks (Non-warrantable) (Figure 29) Figure 29 Leather Steering Wheel Loose Thread, Originates At The Knotted End Of The Thread (Warrantable) (Figure 30) Figure 30 Leather Steering Wheel Cut Thread (Non-warrantable) (Figure 31) Figure 31 Steering Wheel Modification (Non-warrantable) (Figure 32) Figure 32 Steering Wheel Cover Repair (Warrantable) (Figure 33) Can be repaired per the Workshop Manual. Figure 33 © 2023 Ford Motor Company
- 1 reply
-
- 3
-
-
Document Download Link> TSB 23-2075 - 2018-2019 Edge, 2018 MKX, 2019 Nautilus, 2.7L EcoBoost Built On or Before August 1, 2019 - Oil Pan Leaking + Other Models With 2.7L & 3.0L Ecoboost.pdf TECHNICAL SERVICE BULLETIN Oil Pan Leaking - Built On Or Before 15-Aug-2019 23-2075 08 March 2023 This bulletin supersedes 19-2387. Model: Ford 2018-2019 Edge Engine: 2.7L EcoBoost Built on or before 1-Aug-2019 2018-2019 Fusion Engine: 2.7L EcoBoost Built on or before 15-Aug-2019 Lincoln 2018-2019 Continental Engine: 2.7L EcoBoost Engine: 3.0L EcoBoost Built on or before 1-Aug-2019 2018 MKX Engine: 2.7L EcoBoost Built on or before 1-Aug-2019 2018-2019 MKZ Engine: 3.0L EcoBoost Built on or before 15-Aug-2019 2019 Nautilus Engine: 2.7L EcoBoost Built on or before 1-Aug-2019 Summary This article supersedes TSB 19-2387 to update the Part List. Issue: Some 2018-2019 Edge/Continental, 2018 MKX and 2019 Nautilus vehicles built on or before 1-Aug-2019 and 2018-2019 Fusion/MKZ vehicles built on or before 15-Aug-2019 equipped with a 2.7L EcoBoost or 3.0L EcoBoost engine may exhibit an oil leak from the engine oil pan RTV seal. To correct the condition, follow the Service Procedure steps to replace the oil pan with a new oil pan equipped with a press in place gasket. Action: Follow the Service Procedure steps to correct the condition on vehicles that meet all of the following criteria: • One of the following vehicle lines: - 2018-2019 Edge/Continental built on or before 1-Aug-2019 - 2018 MKX built on or before 1-Aug-2019 - 2019 Nautilus built on or before 1-Aug-2019 - 2018-2019 Fusion/MKZ built on or before 15-Aug-2019 • 2.7L/3.0L EcoBoost engine • Oil leak from the engine oil pan RTV seal Parts Service Part Number Quantity Description Unit of Issue Piece Quantity KU2Z-6731-A 1 Oil Filter 1 1 KT4Z-6675-D 1 Oil Pan 1 1 FT4Z-6626-A 1 Oil Pump Seal 1 1 DS7Z-19B596-A 1 A/C O-Rings And Seal Kit 6 2 DL3Z-19B596-B 1 A/C O-Rings And Seal Kit 1 1 Kit W714265-S442 1 Left Catalytic Converter Nuts 4 2 BL3Z-9450-A 1 Left Catalytic Converter Gasket 1 1 W712458-S900 1 Left Catalytic Converter Studs (2019 Edge / Nautilus) 4 2 XO-5W30-Q1SP As Needed Motorcraft® SAE 5W-30 Premium Synthetic Blend Motor Oil (All Markets Except Canada) CXO-5W30-LSP6 As Needed Motorcraft® SAE 5W-30 Super Premium Motor Oil (Canada Only) TA-357 As Needed Motorcraft® High Performance Engine RTV Silicone YN-19 As Needed Motorcraft® R-134a Refrigerant (All Markets Except Canada and Mexico) CYN-19-RB As Needed R-134a Refrigerant (Canada Only) MYN-19 As Needed Motorcraft® R-134a Refrigerant (Mexico Only) YN-35 As Needed Motorcraft® R-1234yf Refrigerant PAG Oil YN-12-D As Needed Motorcraft® PAG Refrigerant Compressor Oil (R-134a Only) XL-1 As Needed Motorcraft® Penetrating and Lock Lubricant XL-2 As Needed Motorcraft® High Temperature Nickel Anti-Seize Lubricant ZC-30-A As Needed Motorcraft® Gasket Remover ZC-31-B As Needed Motorcraft® Metal Surface Prep Wipes ZC-20 As Needed Motorcraft® Engine Shampoo and Degreaser (All Markets Except Canada) CXC-66-A As Needed Motorcraft® Engine Shampoo (Canada Only) PM-4-A As Needed Motorcraft® Metal Brake Parts Cleaner (Compliant With Low Volatile Organic Compound Requirements As Required In Some USA States) PM-4-B As Needed Motorcraft® Metal Brake Parts Cleaner (Not Compliant With Volatile Organic Compound Requirements) Warranty Status: Eligible under provisions of New Vehicle Limited Warranty (NVLW)/Service Part Warranty (SPW)/Special Service Part (SSP)/Extended Service Plan (ESP) coverage. Limits/policies/prior approvals are not altered by a TSB. NVLW/SPW/SSP/ESP coverage limits are determined by the identified causal part and verified using the OASIS part coverage tool. Labor Times Description Operation No. Time 2018-2019 Continental 2.7L/3.0L EcoBoost: Inspect And Replace The Engine Oil Pan (Do Not Use With Any Labor Operations Outside Of This Article) (Can Be Claimed With D Or E And F) 232075A 3.1 Hrs. 2018-2019 Edge, 2018 MKX and 2019 Nautilus 2.7L EcoBoost: Inspect And Replace The Engine Oil Pan (Do Not Use With Any Labor Operations Outside Of This Article) (Can Be Claimed With D Or E And F) 232075B 3.4 Hrs. 2018-2019 Fusion 2.7L EcoBoost, 2018-2019 MKZ 3.0L EcoBoost: Inspect And Replace The Engine Oil Pan (Do Not Use With Any Labor Operations Outside Of This Article) (Can Be Claimed With D Or E And F) 232075C 3.4 Hrs. 2018-2019 Edge/MKX/Continental/Fusion, 2019 Nautilus: Additional Time To Check And Correct Toe Vehicles Without Lane Departure 232075D 0.6 Hrs. 2018-2019 Edge/MKX/Continental/Fusion, 2019 Nautilus: Additional Time To Check And Correct Toe Vehicles With Lane Departure 232075E 0.8 Hrs. 2018-2019 Edge/MKX/Continental/Fusion, 2019 Nautilus: Additional Time When 360 Degree Camera Alignment Is Necessary 232075F 0.5 Hrs. Repair/Claim Coding Causal Part: 6675 Condition Code: D8 Service Procedure CAUTION: Do not use the oil pan with press-in-place gasket on 2015-2017 model year vehicles as this oil pan is not equipped with a positive crankcase ventilation (PCV) check valve. Installation of this oil pan on a 2015-2017 model year vehicle will result in oil consumption which may result in engine damage. 1. Remove and discard the oil pan and oil pump seal. Refer to Workshop Manual (WSM), Section 303-01. 2. Clean and prepare the engine sealing surface. Refer to WSM, Section 303-00. 3. Install the new oil pump seal. 4. Apply a 18 mm (0.708 in) bead of Motorcraft® High Performance Engine RTV Silicone to engine the front cover-to-cylinder block joint areas on the oil pan. (Figure 1) NOTE: The new oil pan does not require the use of Motorcraft® High Performance Engine RTV Silicone in any other location. Figure 1 5. Install the new oil pan. Refer to the WSM, Section 303-01. © 2023 Ford Motor Company Supplemental document download link> Oil Pan - Removal and Installation - 2.7L EcoBoost - 2019 Edge Workshop Manual.pdf
- 1 reply
-
- 2
-
-
Good catch, Omar302! The 2019 Edge SEL Order Guide (edited here for specificity) clearly shows Stop-and-Go as a "new for this model year" Adaptive Cruise Control function... The paragraph you cite in this 2019 Edge Workshop Manual section is included through the current 2022-2023 edition, which shares the same revision date as the 2019 version... So, the quoted paragraph certainly deserves updating to properly describe ACC Stop-and-Go behavior, though at least, AAC stop and go is mentioned in the 2019 Workshop Manual section in relation to Network Input Messages from the Image Processing Module A (IPMA)... Ford would do well to hire you into a Proofreader/Editor position in the Technical Writing Department, which you could likely fulfill remotely, without any need to relocate to Dearborn. Good luck!
-
From the 2020 Edge Workshop Manual... Moving your device cursor over capitalized acronyms should yield an onscreen full-word description. Fog Lamps System Diagram Fog Lamps The front fog lamps can be turned on when the ignition is in ON, by placing the headlamp switch in any position except OFF and pressing the front fog lamp switch. The BCM monitors the headlamp switch position by sending voltage signals on multiple circuits to the headlamp switch. There is one circuit for each headlamp switch position. At any given time, one of the signal circuits is switched to ground to indicate the headlamp switch position. When the BCM receives input from the headlamp switch indicating a request for the front fog lamps, the BCM provides voltage to the front fog lamps. The BCM also provides an Field Effect Transistor (FET) protection of the fog lamp output circuits. When an excessive current draw is detected, the BCM disables the fog lamp output circuit drivers. Fog Lamps Wiring Diagram Turn Signal and Hazard Lamps System Diagram Network Message Chart BCM Network Input Messages Broadcast Message Originating Module Message Purpose Turn signal switch status SCCM Indicates the turn signal stalk position on the LH steering column multifunction switch (left/right lane change or turn signal on or off). The BCM activates the left/right turn signals based on this input. DDM and PDM Network Input Messages Broadcast Message Originating Module Message Purpose Turn indication request BCM A command to the DDM or PDM to activate/deactivate the exterior mirror turn indicator. Turn Signals The SCCM monitors the LH steering column multifunction switch position. When the LH steering column multifunction switch is in the LH TURN or RH TURN position, the SCCM sends a message over the HS-CAN2 to the GWM then the GWM sends the message to the BCM over the HS-CAN1 indicating a request for the LH or RH turn signal. For high series headlamp turn lamps and all rear turn lamps, when the BCM receives a request for a turn signal, the BCM supplies on/off voltage to the appropriate turn lamp Light Emitting Diodes (LEDs). The turn lamps are Light Emitting Diodes (LEDs) and have an outage circuit that tells the BCM when the Light Emitting Diodes (LEDs) are inoperative. During normal operation, when voltage is applied to the turn Light Emitting Diodes (LEDs), the feedback circuit sends the same voltage back to the BCM through the outage circuit. If the Light Emitting Diodes (LEDs) are inoperative the BCM will not receive this voltage feedback through the outage circuit. When the BCM receives a request for a turn signal, the BCM sends a turn indicator command message over the HS-CAN1 to the GWM then the MS-CAN to the door modules for the exterior mirror turn lamps. When the BCM receives a request for a turn signal, the BCM supplies on/off voltage to the appropriate turn lamps. If a front or rear turn signal lamp is inoperative, the IPC turn lamp indicator fast flashes at approximately 150 times per minute to indicate a bulb outage to the driver (the exterior turn lamps will still flash at approximately 70 times per minute). The BCM also provides Field Effect Transistor (FET) protection of the turn lamp output circuits. When an excessive current draw is detected, the BCM disables the affected turn lamp circuit driver. Good luck!
-
My similar curiosity about our 2015 MKX's Adaptive Cruise actuating the vehicle's brake lights was satisfied when driving at night with the second row seats folded down. The CHMSL brake lamp illuminating the cargo area was evident enough in the rear view mirror to put me at ease, that following drivers are sufficiently warned when automatic braking occurs. The following descriptions from the 2019 Edge Workshop Manual on the Adaptive Cruise Control system & the Collision Warning/Collision Avoidance system may enhance your understanding and deepen your confidence in these valuable driver assistance features. Good luck! Moving your device cursor over capitalized acronyms should yield an onscreen full-word description... Cruise Control - System Operation and Component Description System Operation Adaptive Cruise Control Network Message Chart Network Input Messages - ABS Module Broadcast Message Originating Module Message Purpose ACC deceleration request IPMA Used for cruise control automatic braking. ACC stop mode request PCM Used for ACC automatic braking. Brake pedal applied PCM Used for brake switch input. Cruise control overide PCM Driver overriding cruise control with accelerator pedal. Network Input Messages - CCM Broadcast Message Originating Module Message Purpose APP PCM Used for accelerator pedal status. ACC enabled IPC Activates ACC ACC stop mode request PCM Used for ACC automatic braking. ACC switch comands SCCM Used for speed control enable/disable, gap settings and operating mode request. Brake pedal applied PCM Used for brake switch input. Cruise control override PCM Driver overriding cruise control with accelerator pedal. Ignition status BCM Used for ignition switch position input. Stability control event in progress ABS module Deactivates cruise control when requested. Traction control event in progress Vehicle yaw rate Vehicle lateral acceleration RCM Deactivates cruise control when requested. Vehicle longitudinal acceleration Vehicle configuration data BCM Used for comparison checking adaptive cruise control configuration. Network Input Messages - IPC Broadcast Message Originating Module Message Purpose ACC gap distance display IPMA Data used to generate message center display indicating adaptive cruise control gap setting. ACC follow mode display IPMA Data used to activate the follow vehicle indicator. ACC stop mode display IPMA Data used to activate the stop and go auto mode indicator. ACC resume display IPMA Data used to activate the stop and go auto resume mode indicator. Cruise control set speed display PCM Data used to activate the select cruise control display. Cruise control override PCM Driver overriding cruise control with accelerator pedal. Cruise control status PCM Data used for cruise control indicator status. Network Input Messages - PCM Broadcast Message Originating Module Message Purpose Steering wheel switch speed control request SCCM Used for cruise control enable/disable and operating mode request. Stability control event in progress ABS module Deactivates cruise control when requested. Traction control event in progress Vehicle lateral acceleration RCM Deactivates cruise control when requested. Vehicle longitudinal acceleration Vehicle yaw rate ACC Operation NOTE: For a complete illustration of the ACC indicators and graphic displays, refer to the Owner's Literature. The ACC system functions much like a standard cruise control system. The ACC system automatically adjusts the vehicle speed to maintain a set distance gap from the front of the vehicle and the vehicle in the same path of travel. When the ACC system is on and is following a vehicle or a vehicle enters the same driving lane, a follow vehicle graphic is displayed in the message center. The ACC system does not function if the vehicle speed is below 20 km/h (12 mph). As the vehicle slows down during automatic braking, the ACC system discontinues braking at 20 km/h (12 mph). At that speed, an audible alarm sounds and the automatic braking from the ABS module is released. The driver must take over the vehicle braking control. (EDITED by Haz- See subsequent posts, below) The cruise control deactivator switch (which is integral to the BPP switch) is an additional safety feature. When the brake pedal is applied, the cruise control system deactivator switch opens and removes the ground signal from the PCM input circuit, releasing the throttle and immediately deactivating the system. The CCM monitors the yaw rate signal from the ABS module and compares it to the wheel speed and steering wheel angle signals. If the ABS module determines the yaw rate is invalid, the CCM disables the ACC . The message center displays the message COLLISION WARNING MALFUNCTION and/or ADAPTIVE CRUISE MALFUNCTION. The CCM monitors the environment in front of the vehicle while active. If the radar beam is obstructed by a buildup of snow, ice, rain or other debris or the vehicle is driven in a desert environment with no other traffic for extended periods of time, the sensor triggers an "ADAPTIVE CRUISE NOT AVAILABLE SENSOR BLOCKED SEE MANUAL" message in the message center and disables the ACC . The ACC resumes once the obstruction is cleared and the radar is able to detect targets or upon a key cycle. The ACC system does not engage properly if the front radar sensor is not aligned correctly and the message center displays FRONT SENSOR NOT ALIGNED. The ACC resumes once the radar is aligned and is able to properly detect targets. The ABS module estimates brake temperature by monitoring applied brake pressure over a period of time and sends a message to the CCM when the estimated temperature is above a given threshold. An alarm sounds and the ACC system is deactivated until the estimated brake temperature returns to cooler operating conditions. This condition can happen in a hilly or mountainous driving terrain. All CCM Diagnostic Trouble Codes (DTCs) are sent to the IPMA on a dedicated private CAN . The IPMA acts as a gateway. Cruise Control Indicator The ACC indicator located in the IPC illuminates a gray indicator lamp and displays the previous gap setting and SET graphic indicating the systems in standby mode. This notifies the driver the system is ready and the vehicle can be accelerated to the desired speed. A green ACC indicator illuminates when the system is active. Steering Wheel Switch Function The ACC steering wheel mounted switches are momentary contact switches that toggle up and down for the cruise control switch state. Pressing and releasing the steering wheel cruise control ON/OFF switch turns the cruise control system on. Pressing up (SET+) and releasing the SET switch sets the vehicle's speed and stores the set speed in memory. The ACC indicator illuminates and the message center displays the set speed and gap setting graphic. There are two ways to change the set speed. The first way is to accelerate or brake to the desired speed and press and release the SET cruise control switch until the desired set speed is shown on the message center. The second way is by tapping the SET+ or the SET- switch while in the set mode, increasing or decreasing the displayed set speed by 1.6 km/h (1 mph) per tap. If the respective button is pressed and held, the displayed set speed continues to increase or decrease until the button is released. The ACC system may apply the brakes to slow the vehicle down to the new set speed. The set speed displays continuously in the message center while the ACC system is active. Pressing and releasing the OFF switch or switching the ignition to OFF, turns the ACC system off. The ACC set speed memory is erased. Applying the brake or pressing the CNCL switch puts the ACC system in standby mode and the last set speed is displayed in the message center with a strike through. Pressing the RES button when the ACC system is in standby mode causes the vehicle to accelerate to the last set speed. The set speed continuously displays in the message center while the ACC system is active. The RES button does not function if the OFF button is pressed, the ignition is cycled OFF or if the current vehicle speed is below the minimum operational speed. The ACC system has the capability for the driver to change from ACC to standard cruise control. The LH 5-way steering wheel switch is used to switch from the ACC system to standard cruise control system within the message center. For information on selecting the standard cruise control in the message center, refer to Owner's Literature. Once the driver has selected the standard cruise control in the message center, the ACC indicator is replaced by the standard cruise control indicator. The vehicle no longer responds to lead vehicles or automatic braking. Upon the next ignition cycle, the vehicle defaults back to the ACC system. Gap Setting When a vehicle ahead enters the same lane or a slower vehicle is ahead in the same lane, the vehicle speed adjusts automatically to maintain a preset distance gap. A bar graph with four preset distance gap settings are displayed in the message center. Pressing up (decrease) or down (increase) on the steering wheel cruise control gap switch increases or decreases the distance from the vehicle ahead. If all of the bars are illuminated, this is the longest gap setting. If only one bar is illuminated, that is the shortest gap setting. The vehicle maintains the distance gap to the vehicle ahead until: the vehicle ahead accelerates to a speed above the set speed. the vehicle ahead moves out of the lane or out of view. the vehicle speed falls below 20 km/h (12 mph). a new gap distance is set. After each ignition cycle, the previous gap setting is remembered and the system is set to that gap setting. The distance gap can be overridden by applying the accelerator pedal. The follow vehicle graphic is not displayed in the message center and the green indicator illuminates. When the accelerator pedal is released, the ACC system returns to normal operation and the vehicle speed decreases to the set speed or a lower speed if following a vehicle ahead. Deceleration Control The CCM commands the ABS module, which controls the brakes, to automatically apply the brakes to slow the vehicle to maintain a safe distance to the vehicle in front. Pre-Collision Assist System Operation The pre-collision assist system is an additional safety feature on vehicles equipped with ACC . The system is active whether the ACC system is on or off. If the system detects a vehicle, pedestrian or other object in the vehicle path of travel, the system provides three levels of functionality: Visual and audible alert Brake support Active braking The system uses object detection information from the radar sensor integrated in the CCM and the forward-looking camera in the IPMA mounted on the front windshield below the rear view mirror. The CCM and the IPMA scan a designated area in front of the vehicle. Messages are sent between the CCM and the IPMA on dedicated CAN circuit, which determine whether an object, vehicle or pedestrian is in the path of travel, the approximate distance to the object and how fast the vehicle is approaching it. For additional information, Component Description Steering Wheel Switches The cruise control steering wheel mounted switches are momentary contact switches that toggle up and down for the switch state. The switches are an input to the SCCM . Brake Switch When the brake pedal is applied, an electrical signal from stoplamp circuit to the PCM deactivates the system. Under increased brake pedal effort, the cruise control deactivator switch opens and removes the ground signal from the PCM input circuit releasing the throttle, immediately deactivating the system. CCM The CCM contains a radar sensing unit which measures the relative speed and the distance between the front of the vehicle and the vehicle being followed. The IPMA is responsible for requesting the PCM to increase vehicle speed and the ABS module to brake, when necessary. All CCM Diagnostic Trouble Codes (DTCs) are sent to the IPMA on a dedicated private CAN . The IPMA acts as a gateway. IPMA The IPMA is located on the windshield, below the interior rear view mirror. The IPMA contains a forward-looking camera with a designated sight line in front of the moving vehicle. The camera detects and differentiate between an approaching object, vehicle or pedestrian in the path of travel. This information is shared with the CCM on a dedicated private CAN circuit. Collision Warning and Collision Avoidance System - System Operation and Component Description System Operation ACC With Pre-Collision Assist Network Message Chart Network Input Messages - ACM Broadcast Message Originating Module Message Purpose IPC chime IPC Data used to command a warning chime during possible collision event and audio mute so that the warning chime can be heard. Network Input Messages - IPC Broadcast Message Originating Module Message Purpose Collision avoidance and driver support camera status IPMA Data used to command the pre-collision assist system fault status in the message center. Collision avoidance and driver support chime status CCM Data used to command a warning chime that a collision event is possible. Collision avoidance and driver support radar blocked warning CCM Data used to command a radar blocked message in the message center. Forward collision chime request CCM Data used to command warning chime during possible collision event. When this message is received, the IPC sends the audio mute message to the ACM . Forward collision warning message request CCM Data used to command warning chime and messages during possible collision event. Network Input Messages - IPMA Broadcast Message Originating Module Message Purpose Collision avoidance and driver support radar status IPMA Data used to communicate the function status of the camera in the IPMA . Network Input Messages - ABS Module Broadcast Message Originating Module Message Purpose Collision mitigation by braking deceleration request CCM Data used to enable the brakes to slow vehicle speed when the pre-collision assist system determines that a collision is imminent. Collision mitigation by braking brake pre-charge CCM Data used to enable the ABS module to pre-charge the brakes to prepare them for rapid braking by the driver. Pre-Collision Assist System Operation The pre-collision assist system is offered as a camera-only option without ACC . An additional safety feature on vehicles equipped with ACC uses both the CCM (radar) and the IPMA . The system is active whether the ACC system is on or off. If the system detects a vehicle, pedestrian or other object in the vehicle path of travel, the system provides three levels of functionality: Visual and audible alert Brake support Active braking Vehicles equipped with ACC uses object detection information from the radar sensor integrated in the CCM and the forward-looking camera in the IPMA located on the windshield, below the interior rear view mirror. The CCM and the IPMA scan a designated area in front of the vehicle. Network messages are sent between the CCM and the IPMA on dedicated CAN circuits, which determine whether an object, vehicle or pedestrian is in the path of travel, the approximate distance to the object and how fast the vehicle is approaching it. Vehicles equipped without ACC uses object detection information from the forward-looking camera in the IPMA only and is located on the windshield, below the interior rear view mirror. When the vehicle approaches the object, the IPMA sends a message through the GWM to the IPC module to turn on the red pre-collision warning indicator in the message center and to sound an audible alert. The IPMA also sends a message to the ABS module to pre-charge the brakes in order to prepare them for rapid braking. If the system determines that a collision is imminent, an active braking message is sent from the IPMA to the ABS module. The system reduces the gap between the brake pads and discs, applying the brakes to slow vehicle speed without driver intervention. The pre-collision alert system uses image recognition software that differentiates shapes, which allows the system to determine if the approaching object is a vehicle or a pedestrian. If the camera does not recognize the shape as a vehicle or a pedestrian, the system does not provide full function. The system may not work properly at night, in direct or low sunlight, when camera vision is reduced due to weather conditions or due to a blocked CCM radar sensor. If the IPMA camera module is obstructed, the pre-collision system does not respond properly to pedestrians or stationary vehicles and reduces the ability to recognize moving vehicles. Unconventional vehicle types, pedestrians in groups or with complex backgrounds or partly obscured pedestrians may not be detected by the system. The pre-collision assist system is active at speeds above 5 km/h (3 mph) and pedestrian detection is active at speeds up to 80 km/h (50 mph). The pre-collision assist system has three levels of sensitivity detection (HIGH, NORMAL and LOW) that can be changed through the message center display in the IPC . The alert sensitivity is adjusted and active braking can be turned OFF in the IPC . The active braking function reverts back to ON at the next ignition cycle. When a system fault is detected with the pre-collision warning system, the message PRE-COLLISION ASSIST NOT AVAILABLE SENSOR BLOCKED or PRE-COLLISION ASSIST NOT AVAILABLE is displayed in the IPC message center. Component Description CCM The CCM contains a radar sensor unit that determines the distance and relative speed of the vehicle that is in the path of travel. All CCM Diagnostic Trouble Codes (DTCs) are sent to the IPMA on a dedicated private CAN . The IPMA acts as a gateway for the CCM .
-
From the 2016 Edge Workshop Manual... Moving your device cursor over capitalized acronyms should yield an onscreen full-word description. DRL System Diagram Network Message Chart BCM Network Input Messages Broadcast Message Originating Module Message Purpose Gear position PCM Indicates the GSM request to the BCM . When the GSM has selected any position other than park, the BCM activates the DRL . DRL For the halogen headlamp system, the DRL system utilizes the existing circuitry and components from the headlamp low beam system. The DRL system operates the low beam headlamps at a reduced intensity. For the High Intensity Discharge (HID) headlamp system, DRL system utilizes a halogen bulb in the headlamp assembly. The BCM monitors the ignition status, the headlamp switch and autolamp status. There are two types of DRL . Conventional (where it is required) and configurable. When equipped with conventional DRL , the DRL are active in any headlamp switch position except the HEADLAMPS position. When equipped with configurable DRL , the DRL may be enabled through the IPC message center. When enabled, the DRL are active only in the AUTOLAMPS headlamp position. When autolamps request the headlamps on, the DRL are de-activated. The DRL are activated when the following conditions are met: the ignition is in run the headlamps have not been turned on by the autolamp system or the headlamp switch the transmission is not in park When a turn signal is active, the corresponding daytime running lamp will turn off. Once the turn signal is deactivated, the daytime running lamp returns to normal operation. When the transmission is in not in PARK, the PCM sends a message over the HS-CAN1 to the BCM indicating the transmission is not in PARK. The BCM also provides Field Effect Transistor (FET) protection of the exterior lamps switched voltage and DRL output circuits. When an excessive current draw is detected, the BCM disables the affected circuit driver. Field Effect Transistor (FET) Protection The BCM utilizes an Field Effect Transistor (FET) protective circuit strategy for many of its outputs, for example, lamp output circuits. Output loads (current level) are monitored for excessive current (typically short circuits) and are shut down (turns off the voltage or ground provided by the module) when a fault event is detected. A Field Effect Transistor (FET) is a type of transistor that the control module software uses to control and monitor current flow on module outputs. The Field Effect Transistor (FET) protection strategy prevents module damage in the event of excessive current flow. Output loads (current level) are monitored for excessive current draw (typically short circuits). When a fault event is detected the Field Effect Transistor (FET) turns off and a short circuit DTC sets. The module resets the Field Effect Transistor (FET) protection and allows the circuit to function when the fault is corrected or the ignition state is cycled off and then back on. When the excessive circuit load occurs often enough, the module shuts down the output until a repair procedure is carried out. Each Field Effect Transistor (FET) protected circuit has 3 predefined levels of short circuit tolerance based on a module lifetime level of fault events based upon the durability of the Field Effect Transistor (FET). If the total tolerance level is determined to be 600 fault events, the 3 predefined levels would be 200, 400 and 600 fault events. When each level is reached, the DTC associated with the short circuit sets along with DTC U1000:00. These Diagnostic Trouble Codes (DTCs) can be cleared using the module on-demand self-test, then the Clear DTC operation on the scan tool (if the on-demand test shows the fault corrected). The module never resets the fault event counter to zero and continues to advance the fault event counter as short circuit fault events occur. If the number of short circuit fault events reach the third level, then Diagnostic Trouble Codes (DTCs) U1000:00 and U3000:49 set along with the associated short circuit DTC . DTC U3000:49 cannot be cleared and the module must be replaced after the repair. Headlamp Assembly Wiring Diagram - Left Hand Headlamp Assembly Wiring Diagram - Right Hand Good luck!
-
While this General Service Bulletin is written for 2019-2023 Ranger models, it's technique of using a tape measure and masking tape on the steering wheel to measure brake pedal travel does provide a measurement that may be useful when describing brake performance issues to a Dealership Service Rep or Professional Service Technician... GENERAL SERVICE BULLETIN Brake Pedal Travel Measurement Procedure 23-7030 02 March 2023 This bulletin supersedes 22-7059. Model: Ford 2019-2023 Ranger Summary This article supersedes GSB 22-7059 to update the vehicle model years affected. This article is to assist with determining when brake system repairs are necessary to address the symptom of excessive brake pedal travel (low/spongy pedal). Brake Pedal Travel Measurement Procedure 1. With the vehicle on a flat surface, place the transmission selector level in park (P). Do not apply the parking brake. 2. With the engine off, push the brake pedal heavily 10 times. This will remove all vacuum from the brake booster. 3. Pedal travel measurement set up: (1). The steering wheel position will need to be: • Straight/centered with the lower opening at the 6 o’clock position. • Up/down (tilt) position is to be at its lowest point. • In/out (telescoping) position should be at its most inward position (toward the brake pedal). (2). Wrap a 2 inch (5 cm) wide strip of low-tac tape through the lower opening of the steering wheel. (3). Extend a tape measure (in centimeters if available) through the lower opening of the steering wheel over the tape that was just installed. Use caution to prevent any damage to the steering wheel. (Figure 1) Figure 1 (4). Secure the end of the tape measure to the left/center side of the brake pedal as shown. A high-tac tape can be used to hold the end of the tape measure in place during the procedure. (Figure 2) Figure 2 (5). Using a ball point pen, draw a line on the tape to create an indicating mark for the tape measure. (Figure 3) Figure 3 (6). The brake pedal travel measurement set up at the steering wheel should look like this. The actual measurement shown below is only an example and should not be used when calculating pedal travel on the vehicle being tested. (Figure 4) Figure 4 4. Ford Diagnosis and Repair System (FDRS) setup: (1). Connect the FDRS to the vehicle and begin a vehicle session. (2). In the FDRS Menu, access User Settings and make sure that the unit of measure for Pressure is set to kPa. (3). Select the toolbox tab and then datalogger from the list on the right side of the screen. (4). On the datalogger module selection screen, select Anti-lock Brake System (ABS) module and Continue. (5). On the parameter identification (PID) list selection screen for the ABS module, select: BRKHYDPRESS. 5. Brake pedal travel measurement: (1). With the brake pedal not-pressed, record the reading of the tape measure at the line draw on the tape on the steering wheel. (Figure 4) (2). While monitoring the BRKHYDPRESS PID in FDRS, slowly press the brake pedal until 1000 kPa is obtained. (3). Record the reading of the tape measure at the line drawn on the tape on the steering wheel while the brake pedal pressure is being held at 1000 kPa. (4). Perform this test a total of 5 times with 30 second intervals after each press of the brake pedal. Document all readings in the chart provided below. (Table 1) Table 1 Test Number Brake Pedal Not Pressed Measurement (cm) Brake Pedal Pressed Measurement (cm) Calculated Brake Pedal Travel (cm) 1 2 3 4 5 Brake pedal travel average: 6. Is the average brake pedal travel equal to or less than 5.2 cm? (1). Yes - brake pedal travel is within normal range and the brake hydraulic system is operating normally. (2). No - perform a Brake System Pressure Bleeding, refer to Workshop Manual (WSM), Section 206-00 and retest. If the average brake pedal travel is still above the normal range after performing the Brake System Pressure Bleeding procedure, refer to WSM, Section 206-00 for further diagnosis and testing. © 2023 Ford Motor Company All rights reserved. NOTE: This information is not intended to replace or supersede any warranty, parts and service policy, workshop manual (WSM) procedures or technical training or wiring diagram information.
-
GENERAL SERVICE BULLETIN Adaptive Cruise, Pre-Collision And Collision Avoidance System Functionality Diagnostics 23-7031 02 March 2023 This bulletin supersedes 22-7034. Summary This article supersedes GSB 22-7034 to update the Service Information and vehicle model years affected. This article is intended to aid in the diagnosis for vehicles with difficulty resolving image processing module A (IPMA) or cruise control module (CCM) alignment and/or functionality concerns. Service Information Adaptive cruise control and collision avoidance systems can use a forward windshield camera only IPMA or a combination of IPMA and a CCM. Make sure which system is present on the vehicle so the system evaluation is completed properly. The forward collision system warning indicator will be illuminated when the vehicle is in transport mode. Prior to any diagnosis, be sure the vehicle is not in transport mode. For further information on transport mode, Refer to Workshop Manual (WSM), Section 419-10. NOTE: Follow the Service Procedures to troubleshoot IPMA and CCM alignment issues before replacing the parts. For Mustang Mach-E and F-150 vehicles equipped with base part number 14G647, alignment and blockage issues are specific to the sensors and not the electronic control unit (ECU). IPMA (near rear view mirror) forward windshield camera (Figure 1) Figure 1 CCM (in the front grille, either visible or behind bumper) RADAR sensor (Figure 2) Figure 2 NOTE: Environmental factors such as sun position, glare, moisture, frost, snow, ice, and dust/dirt can interfere with system vision and may cause the system to become inactive with a warning until these items clear. If the IMPA/CCM alignment procedure is not successful, inspect for the presence of outside factors. Possible outside factors that may affect IPMA alignment 1. Diagnostic trouble codes (DTCs) other than C1001:54, C1001:78, C1001:97 present in IPMA or other modules (1). Repair all other DTCs prior to diagnosing or attempting IPMA alignment 2. Unclear road markings 3. Module or circuit concerns 4. Accessories blocking camera view, including but not limited to: (1). Snow plow (2). Winch (3). Bug guard 5. Vehicle ride height - refer to specifications in Workshop Manual (WSM), Section 204-00 (1). Vehicle squatting from cargo weight (2). Lift kit (3). Lowering kit (4). Leveling kit (5). Incorrect tire size (6). Other modifications that affect vehicle ride height or stance (7). Incorrect wheel arch measurements input in Interactive Diagnostic System (IDS)/Ford Diagnosis and Repair System (FDRS) 6. Inspect windshield (1). If this concern began after a recent windshield replacement, inspect the replacement windshield for imperfections and correct installation (2). Aftermarket windshield installed • Carlite replacement windshield recommended (3). Windshield clean of moisture, snow, ice, frost, and dust/dirt (4). IPMA lens clean (5). Aftermarket tinting or windshield banners/stickers (6). Glass distortion can distort the camera’s view and prevent camera alignment and functionality (Figure 3) Figure 3 (7). IPMA mounting and/or bracket off-center, not clocked properly or not secured to windshield (Figures 4-5) Figure 4 Figure 5 (8). Windshield not installed correctly. Figure 6 shows a windshield that is recessed near the vehicle’s roof, causing the camera to be pitched upward. Figure 6 Possible outside factors that may affect CCM alignment 1. DTCs present in CCM or other modules Repair all DTCs prior to diagnosing or attempting CCM alignment 2. Module or circuit concerns (usually DTCs would be present) 3. CCM radar blocked - may result in CCM DTC C1A67:97 Figure 7 Inspect the front bumper or CCM location for snow, ice, dust/dirt (Figure 7) (1). Incorrect front license plate/bracket mounting (2). Aftermarket or incorrect bumper or grille (3). Brush guard installed (4). Snow plow or snow plow mounting hardware installed (5). Other aftermarket accessories installed on front of vehicle (Figure ? Figure 8 (6). CCM mounting hardware bent or damaged or improper CCM mounting (Figure 9) NOTE: Improper CCM mounting may also result in DTCs B142E:78 or B1432:78 in the CCM Figure 9 (7). Facia damaged, facia installed incorrectly, or aftermarket facia installed. 4. Using the FDRS tool, check the parameter identification (PID) for ALGN_OFF -CCM. A value greater than +/-3 degrees indicates a mounting issue with the CCM, not necessarily a defective module. Check for CCM or mounting surface damage. If found repair damage as necessary. If no damage found, perform the CCM alignment procedure per WSM Section 419-03, Cruise Control Radar Alignment. CCM Alignment Incorrect If an issue remains after addressing outside factors, perform the CCM alignment procedure. Refer to WSM, Section 419-03, Cruise Control Radar Alignment. Notes regarding radar drive alignment 1. The radar needs to see 150-200 stationary targets on either side of the road to identify the center of the lane. 2. These targets increment as the vehicle is driving over 15 mph (24 km/h). 3. The faster it sees these targets the faster it will complete the process. 4. Loss of communication and internal fault DTCs will prevent completion of the process. 5. Key cycles between initiation of the drive alignment and the drive will move the vehicle out of alignment mode. © 2023 Ford Motor Company All rights reserved. NOTE: This information is not intended to replace or supersede any warranty, parts and service policy, workshop manual (WSM) procedures or technical training or wiring diagram information.
-
Welcome to the Forum! For the TSB Service cost to be covered, per the TSB, some element of Warranty needs to be in force.... Warranty Status: Eligible under provisions of New Vehicle Limited Warranty (NVLW)/Service Part Warranty (SPW)/Special Service Part (SSP)/Extended Service Plan (ESP) coverage. Limits/policies/prior approvals are not altered by a TSB. NVLW/SPW/SSP/ESP coverage limits are determined by the identified causal part and verified using the OASIS part coverage tool. You may want to look at the mileage intervals of your Edge's past oil pan replacements, and then contact your dealer with your Edge's current mileage to get a cost estimate of performing the TSB Service without any Warranty coverage, to better inform your sell/keep decision -- or extend your ESP coverage before it expires. Good luck!
-
SSM 51385 2019-2023 Edge/Nautilus - 2.0L - Repeat Block Heater Failure - Updated Procedure In The Workshop Manual (WSM) Some 2019-2023 Edge/Nautilus vehicles equipped with a 2.0L engine may exhibit a repeat block heater failure. This may be caused by air in the engine cooling system. The WSM replacement procedure has been updated to include the Engine Cooling System Draining, Vacuum Filling and Bleeding procedure found in Section 303-03A Engine Cooling - 2.0L EcoBoost (184kW/250PS) – MI4, General Procedures as the final step. The block heater should not be tested unless all the air has been removed from the engine cooling system following this procedure. Document download links> Block Heater - Removal and Installation - 2.0L EcoBoost - 2023 Edge Workshop Manual.pdf Engine Cooling System Draining, Vacuum Filling and Bleeding - 2.0L EcoBoost - 2023 Edge Workshop Manual.pdf Link to 2.0L EcoBoost Engine Block Heater on Ford's online parts website...
-
SSM 51381 2021-2023 Various Vehicles - Tire Sidewall Wavy/Indentation Appearance Some 2021-2023 Ford and Lincoln vehicles may experience a tire sidewall wavy/indentation appearance in the radial direction on one or both sidewalls. Sidewall wavy/indentation appearance is a common cosmetic characteristic of radial tire construction and will not affect the performance of the tire. Non-Ford supplemental document download> Tire Information Service Bulletin - Vol 21 No 4 - US Tire Manufacturers Association.pdf
-
Released on February 14, 2023... SSM 51360 2021-2023 Edge Titanium/Nautilus - Unintended Hands-Free Liftgate Activation Some 2021-2023 Edge Titanium/Nautilus vehicles equipped with hands-free liftgate may exhibit unintended liftgate activation when coming in contact with the rear bumper cover when the passive key is located in the rear bumper detection area. This is a normal condition and repairs are not necessary. Switching the hands-free liftgate feature off through the vehicle settings or keeping the passive key away from the rear bumper detection area during these actions will prevent unintended activation from occurring. Refer to the Owner’s Manual Power Liftgate section for more details. It is worth noting that 2021-2023 Edge/Nautilus Owner's Manual sections covering Power Liftgate do not include any passage relating to "Switching the hands-free liftgate feature off through the vehicle settings" as mentioned in SSM 51360. The Owner Manuals do include... and... Good luck!
-
GSB 23-7003 - Various Vehicles - Paint And Bumper Concern Analysis
Haz replied to Haz's topic in Recalls, TSBs & Warranty
Document download link> 2017 Model Year Warranty Guide - Version 3 - August 2016.pdf From page 16 of 41 in the PDF... Extended warranty coverage periods are available for certain vehicle parts and conditions. Specifically, (3) Your vehicle’s body sheet metal panels are covered for an extended Corrosion Coverage Period, which lasts for five years, regardless of miles driven. The extended warranty coverage only applies if a body sheet metal panel becomes perforated due to corrosion during normal use due to a manufacturing defect in factory-supplied materials or factory workmanship. If aluminum body panels have corrosion or rust damage, and the damage is not the result of abnormal usage, vehicle accident, customer actions and/or extreme environmental conditions, the corrosion or rust damage repairs are covered for 5 years, unlimited miles. For damage caused by airborne material (environmental fallout) where there is no factory-related defect involved and therefore no warranty - our policy is to provide free repair of paint damage due to the airborne material for 12 months or 12,000 miles, whichever occurs first. Good luck! -
Released on January 23, 2023... SSM 51314 2021-2023 Mustang Mach-E/F-150/Edge/Nautilus, 2022-2023 Expedition/Navigator/Bronco, 2023 Escape/Transit/Corsair - DTC U3000:57 - Unable To Clear Some 2021-2023 Mustang Mach-E/F-150/Edge/Nautilus, 2022-2023 Expedition/Navigator/Bronco, 2023 Escape/Transit/Corsair vehicles may exhibit a diagnostic trouble code (DTC) U3000:57 stored in the accessory protocol interface module (APIM), telematics control unit (TCU), and/or gateway modules (GWM) that will not clear. The presence of this DTC means that an engineering analytic token is present on the vehicle. This analytical token does not affect module functionality or features used by the customer. No attempts should be made to repair this DTC.
-
GENERAL SERVICE BULLETIN Various Vehicles - Paint And Bumper Concern Analysis 23-7003 18 January 2023 This bulletin supersedes 22-7023. Summary This article supersedes GSB 22-7023 to update the Service Information. This article is designed to provide examples of paint conditions / damage to assist in determining if the condition is warrantable / non-warrantable. Refer to the latest version of the Warranty and Policy manual for the latest paint damage warranty coverage. Paint damage is only warrantable on the original factory paint. Use this document to assist in determining warrantable paint concerns. Service Information Ford Motor Company recommends that when resolving customer paint finish appearance concerns, every effort should be made to preserve the factory paint and corrosion protection. Repairing or improving paint finish appearance concerns with touch-ups and polishing techniques should be considered whenever possible as an alternative to removing and refinishing painted surfaces. Minor imperfections in sheet metal seams (inside door areas, inside liftgates, tailgate and under hood areas) can be considered normal in some situations. Efforts to repair or refinish these areas for minor cosmetic defects may compromise or remove the factory corrosion protection and may cause long-term durability concerns. Make sure the vehicle owner is aware of these conditions before attempting repairs. Environmental damage can be removed by following the Environmental Fallout Procedure detailed in Section 501 of the Workshop Manual. Once the environmental damage is removed, buffing and polishing may be required. According to the Owner’s Manual, owners are expected to wash and wax their vehicle regularly, including the bumper system, to remove harmful deposits from the vehicle’s surfaces to help protect the finish. Clean the chrome and stainless steel parts with polish to prevent rust or corrosion. IMPORTANT: Follow the guidelines within the vehicle’s Owner's Manual when cleaning chrome and/or stainless steel parts. Non-warrantable Conditions • Surface rust and deterioration of paint, trim, and appearance items that result from use and/or exposure. • Dents, dings, scratches, nicks, chips, punctures, bird and/or bee droppings, tree sap, road salt. • Normal paint deterioration due to exposure. • Underbody surface rust on frame or chassis components on vehicles reported as sold. Warranty Conditions • Bumper under-chrome defects; thin or peeling chrome. • Paint runs, over spray, sags, blistered / peeling paint. • Excessive dirt specs in paint. • Thin paint, orange peel. • Wavy sheet metal, file, grinder or weld marks. • Outward sheet metal dents. • Surface corrosion with no impact present is covered under the New Vehicle Warranty. The Corrosion Warranty also covers surface corrosion on aluminum body panels, however steel body panels would require sheet metal perforation caused by naturally occurring corrosion. - NOTE: See the Warranty and Policy Manual for more information and for specific coverages. • Iron oxide (rail dust) or acid rain. - NOTE: Although not a factory defect, damage caused by airborne material / environmental fallout damage (such as rail dust or acid rain) to exterior finish has limited coverage according to the Warranty and Policy Manual. Refer to the OWS User Guide for correct claiming sub code Dirt In The Finish (Warrantable) Dirt, sealer, and other debris trapped during the factory finish application. (Figures 1-2) Figure 1 Figure 2 Impact (Chips, Dents, Etc.) (Non-warrantable) Impact damage causing removed finish, substrate damage, and jagged edges. (Figures 3-4) Figure 3 Figure 4 Peeling (Warrantable) Peeling (without damage) to indicate an adhesion defect. (Figures 5-6) Figure 5 Figure 6 Peeling/Cracking Paint (With Damage) (Non-warrantable) Peeling or cracks occur from stress due to impact or flexing of the substrate. (Figures 7-8) Figure 7 Figure 8 Runs/Thin Paint (Warrantable) Causes include excessive or lack of material. (Figures 9-10) Figure 9 Figure 10 Stains (Non-warrantable) Stains may exhibit a drip pattern from abrasive liquids. Etching cannot be felt and will appear dull. (Figures 11-12) Figure 11 Figure 12 Orange Peel, Popping (Warrantable) Small texture differences best seen in a reflection of light. (Figures 13-14) Figure 13 Figure 14 Abrasion, Wear (Non-warrantable) Impact and abrasion. (Figures 15-16) Figure 15 Figure 16 Paint Color Variation (Warrantable) Normal variations are seen with different substrates but color differences should not be noted from all angles. (Figures 17-18) Figure 17 Figure 18 Etching From Abrasives Including Environmental (Non-warrantable) Bird and bee droppings, tree sap. Etching (discolored) cannot be felt. Cracking/removed finish. (Figures 19-20) Figure 19 Figure 20 Environmental Fallout (Limited Coverage) Although this is not a factory defect, damage caused by airborne material / environmental fallout (such as rail dust or acid rain) to exterior finish has limited coverage outlined in the Warranty and Policy Manual. Refer to the OWS User Guide for correct claiming sub code and the Workshop Manual for the environmental fallout removal procedure. (Figures 21-22) Figure 21 Figure 22 Corrosion (Warrantable) Surface corrosion with no impact present is covered under the New Vehicle Warranty. (Figures 23-24) The Corrosion Warranty also covers surface corrosion on aluminum body panels, however steel body panels would require sheet metal perforation caused by naturally occurring corrosion. See the Warranty & Policy Manual for more information. Figure 23 - Steel body panels - corrosion with no perforation (warrantable under New Vehicle Warranty only) Figure 24 - Aluminum body panels - corrosion (warrantable under New Vehicle and Corrosion Warranty with no perforation requirement) Corrosion (Non-warrantable) Surface corrosion which can be removed with cleaning. (Figure 25) Corrosion caused by damage. (Figure 26) Figure 25 Figure 26 Rust Perforation (Warrantable) Rust damage resulting in perforation (holes). Figure 27 - Steel body panels - corrosion with perforation (covered under the Corrosion Warranty) Mechanically Caused Perforation (Non-warrantable) Corrosion must be naturally occurring. (Figure 28) Figure 28 Previous Repair (Non-warrantable) Indicated by peeling paint atop the same/different color. Visible body filler. (Figures 29-30) Figure 29 Figure 30 Clear Coat Peeling (Non-warrantable) The factory paint process bonds color and clear coats together preventing clear coat peeling. (Figures 31-32) Figure 31 Figure 32 © 2023 Ford Motor Company All rights reserved. NOTE: This information is not intended to replace or supersede any warranty, parts and service policy, workshop manual (WSM) procedures or technical training or wiring diagram information.
-
Welcome to the Forum! Document download links> Body Control Module (BCM) - Diagnosis and Testing - 2014 Edge Workshop Manual.pdf Body Control Module (BCM) - Removal and Installation - 2014 Edge Workshop Manual.pdf If your Edge is disabled and you need to get it back on the road, locating an A-graded used Body Control Module (BCM) from a local Salvage Yard at 25%-to-50% of the new part cost using the Car-Part.com search engine may be worthwhile... Good luck!
-
Fluttering Noise from Undercarriage and Dashboad Rattle
Haz replied to CCMAYES72's topic in Brakes, Chassis & Suspension
From the 2019 Edge Workshop Manual... The stamped sheet metal hex nut is also described online as a speed nut. I was unable to pick off the fastener part number from FordParts.com, though a dealership parts staffer will likely find it. On the other hand, providing 1004ron's photo to a local or national-brand auto parts store or hardware store may provide the part quicker and cheaper. Good luck!- 90 replies
-
- 1
-
-
- dash noise
- dash rattle
-
(and 4 more)
Tagged with:
-
The 2022 Edge Workshop Manual offers this Auto-Start-Stop operational description and lists the conditions under which Auto-Start-Stop will not function... Auto-Start-Stop System The Auto-start-stop system helps reduce fuel consumption by automatically shutting off the vehicle’s engine while the vehicle is at a complete stop and restarting the engine when the brake pedal is released. The system can be disabled through the auto-start-stop control switch on the instrument panel centerstack. The Auto-start-stop system is automatically enabled whenever the ignition is turned on. The engine automatically restarts when: the brake pedal is released. the Auto-start-stop system is disabled through the auto-start-stop control switch on the instrument panel centerstack. the battery has a low state of charge. it is necessary to maintain interior comfort. the blower fan speed is increased or the climate control temperature is changed. an electrical accessory is turned on or plugged in. there is low brake vacuum. The Auto-start-stop system may not turn the engine off under these conditions: the HVAC system is in A/C, heat or defrost modes. the rear defroster is on. the battery has a low state of charge. the battery temperature is below 5°C (41°F) or above 60°C (140°F). the engine temperature is below 46°C (115°F). the engine temperature is below 60°C (140°F) and the HVAC system is in heat mode. the gear selector is not in Drive or Sport Mode. the steering wheel is turned rapidly or is at a sharp angle. vehicle speed of greater than 4 km/h (2.5 mph) for more than 2 seconds has not occurred. the vehicle is on a steep road grade. elevation is approximately above 3,048 meters (10,000 feet). Good luck!
-
Welcome to the Forum, Skipper96. Parasitic battery drain diagnostic reference... Document download link> Parasitic Battery Drain Job Aid.pdf Good luck!
-
Because your Edge is exhibiting several Power Liftgate symptoms -- change in open/close velocity; a sporadic failure to pulldown and/or latch; cargo area pushbutton opens but does not close while exterior pushbutton performs normally -- the best-first step may be to perform the Power Liftgate Initialization procedure, which involves de-powering the Rear Gate Trunk Module (RGTM)... Document download link> Power Liftgate Initialization - 2016 Edge Workshop Manual.pdf You will notice this RGTM de-powering can be done either by pulling the RGTM fuses or by disconnecting the Edge's battery. If you choose pulling fuses, there are two -- F76 in the Battery Junction Box (BJB) and F10 in the Body Control Module (BCM)... Battery Junction Box (BJB) Images Release the tabs. Lift and position the top part of the junction box aside. Body Control Module (BCM) Images de-powering Be aware that the alternative RGTM de-powering method -- Battery Disconnect procedure -- offers these cautions... NOTICE: Removing the negative battery ground cable at the LH strut tower will not disable the vehicle's electrical system. Failure to disconnect the battery cable from the battery post may cause component damage. NOTE: When the battery is disconnected and connected, some abnormal drive symptoms may occur while the vehicle relearns its adaptive strategy. The vehicle may need to be driven to allow the PCM to relearn the adaptive strategy values. Document download link> Battery Disconnect and Connect - General Procedures - 2016 Edge Workshop Manual.pdf The following Workshop Manual section provides a wonderful explanation of Power Liftgate operation in conjunction with the RGTM and other components... Document download link> Power Liftgate System - Description and Operation - 2016 Edge Workshop Manual.pdf Please report back on the outcome of the Power Liftgate Initialization procedure. Good luck!
-
The following is a PDF document download link to the relevant section from the Edge Workshop Manual... Windshield Wiper Pivot Arm - Removal and Installation - 2022-2023 Edge Workshop Manual.pdf It includes this guidance, which the windshield installer may not have done... Installation NOTICE: The ignition switch must be set to the ON position. Power is required to hold the wiper motor in the PARK position. No power or low battery voltage will allow the motor to move from the PARK position during the torquing operation resulting in incorrect wiper arm position. Good luck!